Selecting the right hydraulic hose connector is important to have a reliable and efficient hydraulic system.
Understanding the types of hydraulic hose connectors, their materials, and compatibility factors will save you time, money, and potential headaches.
This guide will help you navigate hydraulic hose connectors and make informed decisions when selecting, installing, and maintaining these components.
Key Takeaways
- Understanding the function and importance of hydraulic hose connectors is important for selecting the right one.
- Different materials, compatibility, pressure rating and performance has to be considered when choosing a connector.
Understanding Hydraulic Hose Connectors
Hydraulic hose connectors play a vital role in joining hydraulic hoses to pipe, equipment, and other hoses, enabling quick connection and disconnection without the use of tools.
They also provide sealing and protection to the ends of hoses, guarding against contaminants like dust and dirt.
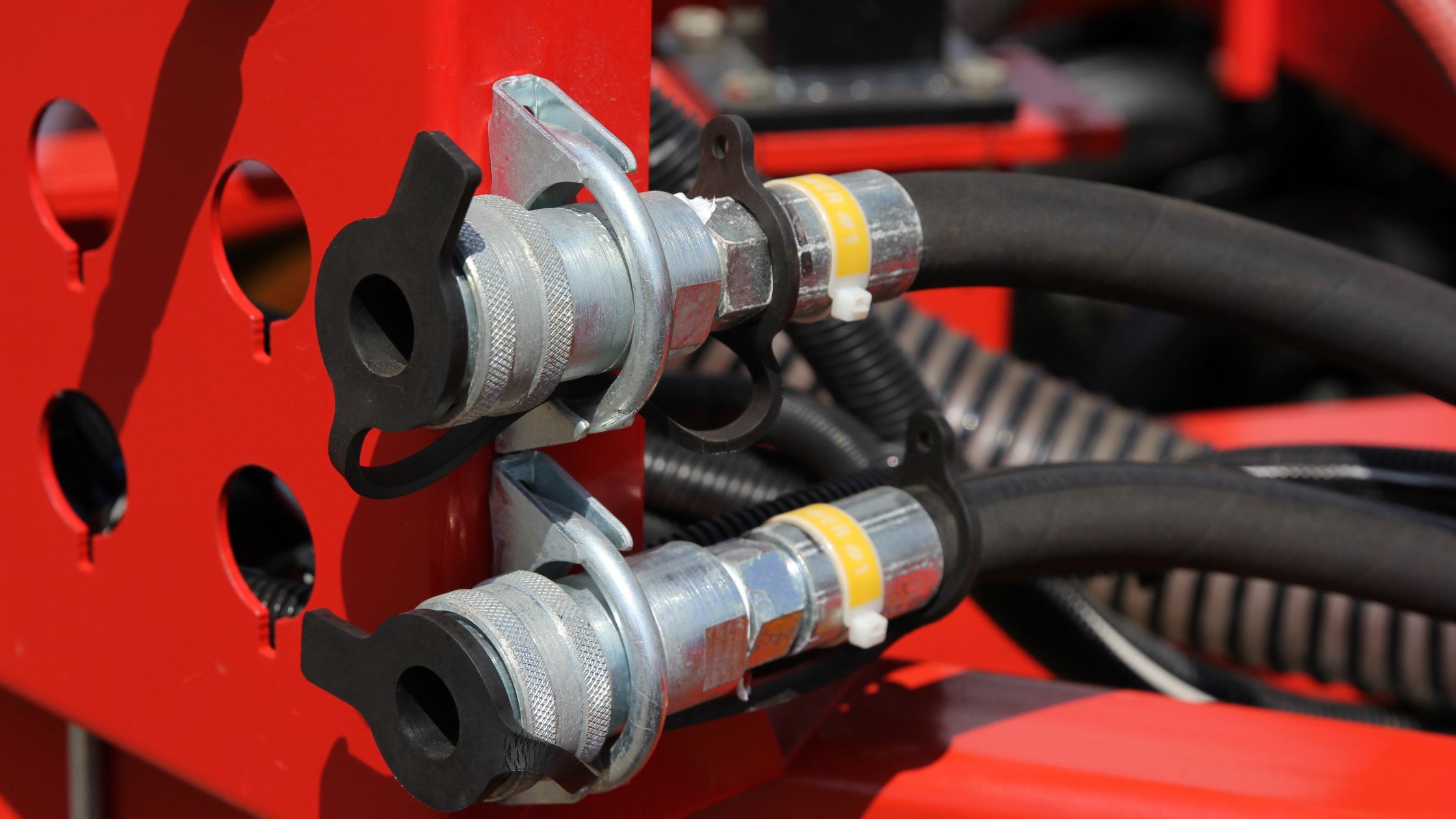
Choosing the right connector provides an extended service life and leak-free performance for your hydraulic hose assemblies.
Types of Hydraulic Hose Connectors
A wide array of hydraulic hose connectors is available to suit various applications, including metal seal connectors, soft seal connectors, tapered thread connectors, O-Ring fittings, and face-seal (flat-face) O-Ring fittings.
Some common types of connectors include crimped and push-lock connectors, each offering its own set of advantages and applications.
Crimped connectors are permanently sealed onto a hydraulic hose using a crimping machine, providing a dependable and leak-proof connection.
Push-lock connectors are field attachable and enable the swift and effortless assembly of hydraulic hoses without the need for clamps or crimp sleeves.
Materials Used for Connectors
The materials used for hydraulic hose connectors impact their performance and durability. Steel, stainless steel, and brass are the most commonly used materials due to their varying levels of durability, corrosion resistance, and compatibility with various fluids.
Stainless steel hose fittings offer excellent corrosion resistance, making them ideal for harsh environments.
Brass, on the other hand, provides strength, corrosion resistance, and good ductility at high temperatures, making it a popular choice for general-purpose applications.
Steel connectors offer remarkable corrosion resistance, elevated strength, and durability, as well as the ability to withstand high pressures and temperatures, making them suitable for a wide range of hydraulic applications.
Selecting the Right Connector for Your Hydraulic Hose
The selection of a hydraulic hose connector requires consideration of compatibility with the hose type, pressure rating, and overall performance.
A fitting that is both suitable for the hose material and fluid, and consistent in size with the hose, aids in preventing leaks and system malfunctions. Hydraulic hose fittings play a big role the performance of the system.
Compatibility with Hydraulic Hoses
Factors such as pressure rating, material, diameter, thread/connection type, size, temperature rating, flow rate, and hose compatibility must be considered with the compatibility of hydraulic hose connectors.
Mismatched hydraulic hose connectors can have a detrimental effect on the performance of the hydraulic system, including leaks and bursts, pressure losses, improper flow, and incompatibility.
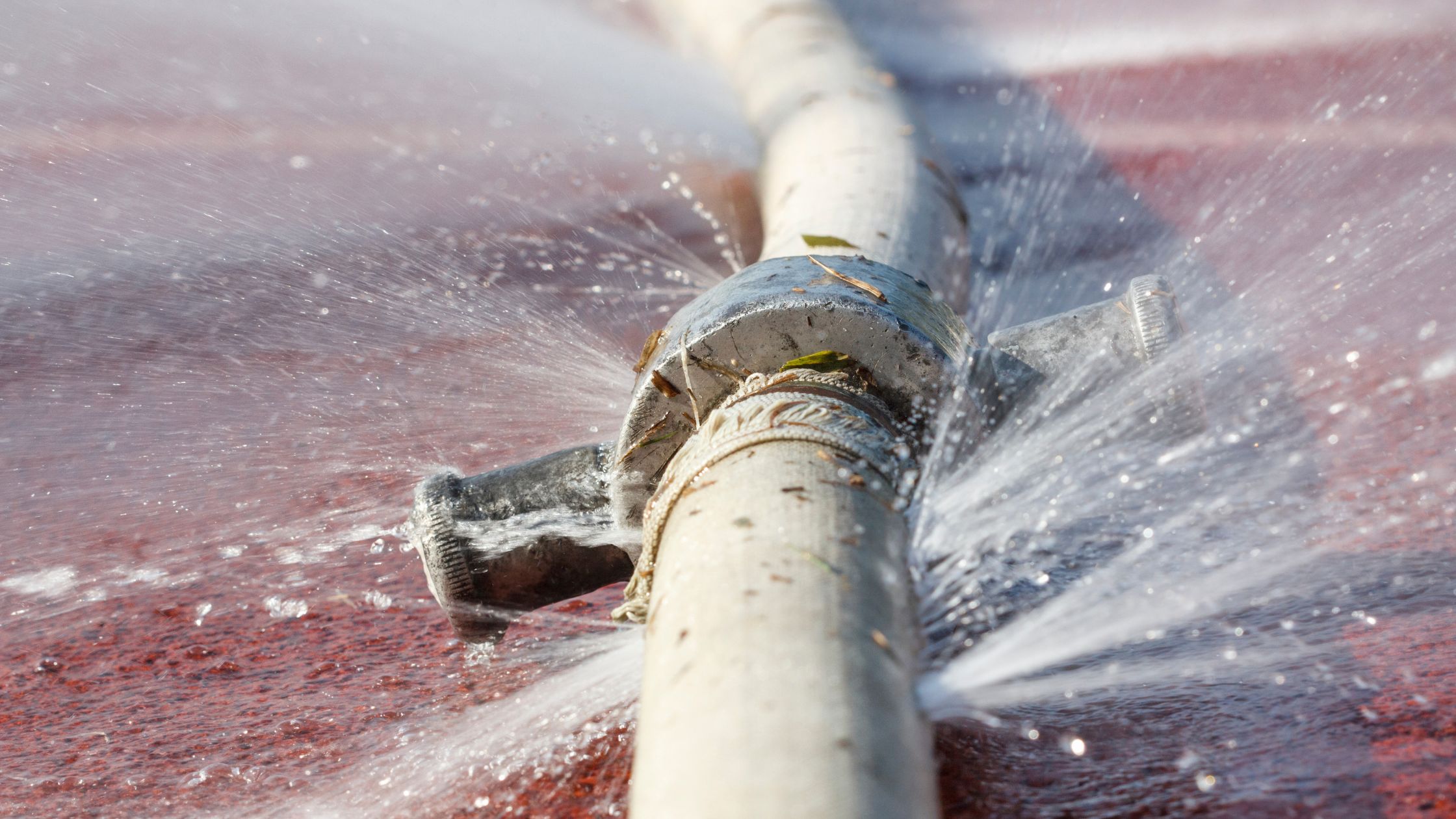
Compatibility and proper matching of hydraulic hose connectors are indispensable for attaining optimal performance and safety of the hydraulic system. This requires selecting a connector that is suitable for the specific type of hydraulic hose and fluid being used.
Pressure Rating and Performance
The pressure rating of a hydraulic connector has a big effect on its performance and should not be overlooked when selecting a connector for your system. Typical pressure ratings for hydraulic hose connectors range from 3,000 to 5,000 psi (pounds per square inch).
Exceeding the pressure rating can lead to:
- Fluid loss
- Component failure
- Machine downtime
- Hose bursting
- Hose coupling blow-off
- Catastrophic incidents
- Environmental contamination
- Potential operator injuries
Choosing a connector with a maximum pressure rating that equals or exceeds the operating pressure of the hydraulic system is key for optimal performance and safety.
Hydraulic Hose Assemblies: Best Practices
Following best practices for hydraulic hose assemblies, such as proper installation techniques and preventative maintenance, can help extend the life of your connectors and hoses, prevent site damage, abrasive wear, and prolonged exposure to heat and ultraviolet rays.
The service life and performance of your hydraulic hose assemblies can be improved through the following measures:
- Using hose whip restraints
- Maintaining proper installation and routing
- Avoiding tight bending
- Checking and tightening fittings
- Proper storage
Proper Installation Techniques
A secure and leak-free connection between your hydraulic hose and connector relies on proper installation techniques. The correct tools for proper installation include:
- Flare nut wrench
- Reusable hydraulic hose tools
- Fitting insertion tools
- Hydraulic hose relief tool
- Hose press
Adhering to the manufacturer’s instructions for the reusable hose fittings in use is important, as installation methods may differ slightly.
The type of hydraulic hose connector can affect the installation process, determining the method of attachment, ease and speed of installation, and the durability and reliability of the connection.
Preventative Maintenance and Emergency Repairs
For the optimal performance of hydraulic hose assemblies, regular preventative maintenance is a necessity.
Routine inspection of hoses and fittings for wear, damage or leaks can preemptively identify potential issues. Monitoring the hydraulic fluid levels and pressure to make sure they are within the recommended range can help maintain the efficiency and safety of the system.
During emergency repairs, shutting off the system’s power, inspecting the hose and connectors for damage, and promptly replacing any damaged components is of vital.
Having the necessary tools for upkeep and repair, such as wrenches, an adapter, a utility knife, hose cutters, a hose crimping machine, safety goggles, and gloves, on hand can minimize downtime and prevent costly damage to your hydraulic system.
Summary
In conclusion, selecting the right hydraulic hose connector is key for optimal performance and longevity of your hydraulic system. Understanding the various types of connectors, their materials, compatibility factors, and best practices for installation and maintenance can help you make the right choice for your specific application.
Reach out to TT Weber Hydraulic for any hydraulic questions you have!