Hydraulic cylinders are integral to many industrial and mobile applications because they convert pressurized fluid into linear motion.
To get the most out of these tools, it’s essential to know all about their components and the different types that are available. You also need to know how each part works together in order for the cylinder to function properly with maximum performance.
Key Takeaways
- Understand the components of a hydraulic cylinder for effective operation and maintenance.
- Learn about different types of cylinders and how to select the right one for your application.
- Consider working with an experienced supplier or manufacturer to ensure optimal performance, efficiency, and life span.
Understanding Hydraulic Cylinder Components
A thorough comprehension of the components that make up a hydraulic cylinder is fundamental if you want to operate one properly and effectively.
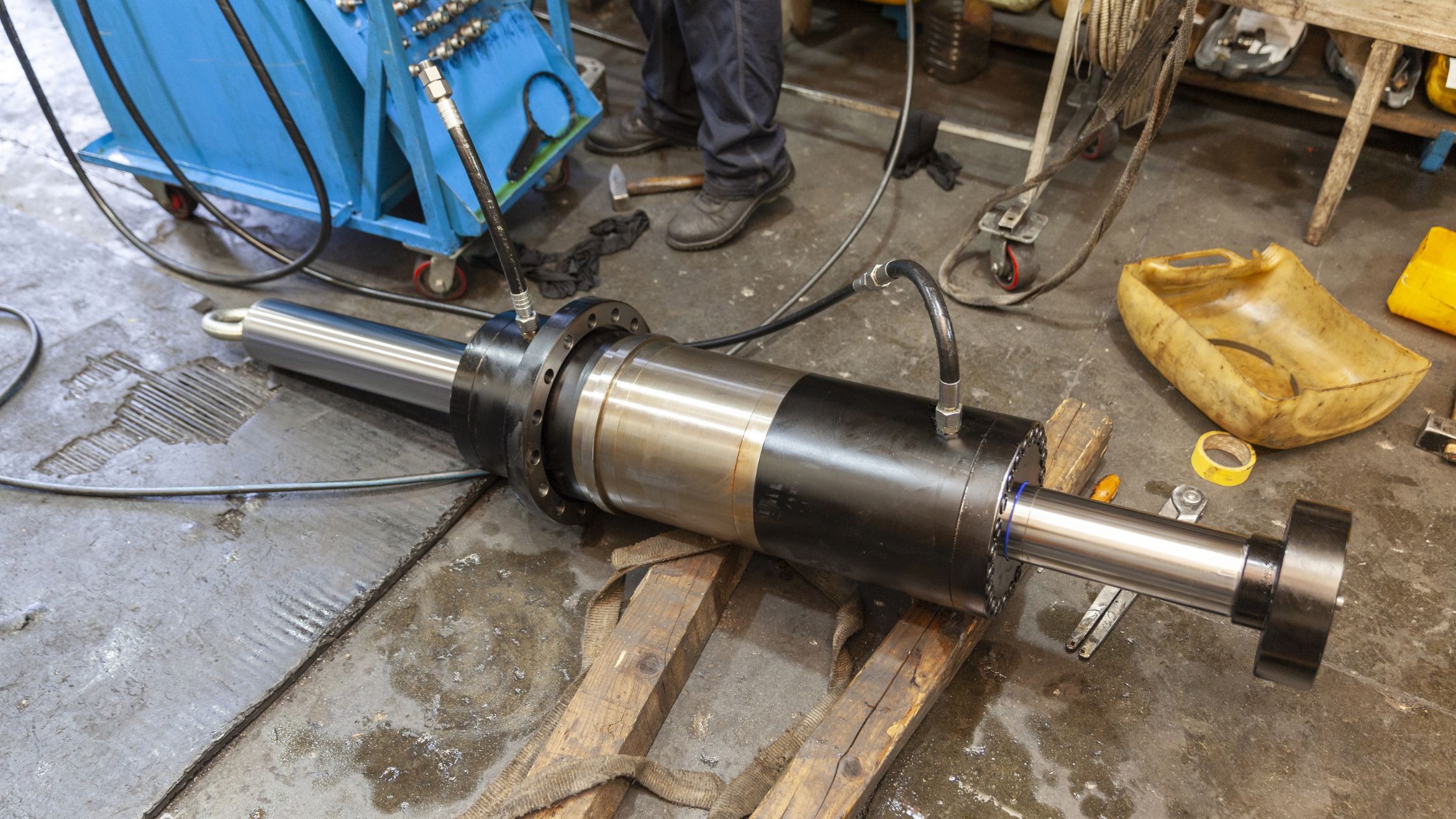
Cylinder barrel: This component holds together other elements that compose the overall structure. It keeps them aligned so they operate efficiently as one unit.
Piston rod: Essentially providing stability, the piston rod connects the piston to the head/base plate areas. It allows motion in only one direction with the necessary strength to maintain good shape under pressure thrusts generated by the flow of fluid inside the pipe.
Cylinder head and base: The head and base plates serve the same purpose. In combination with seals or glands that are fitted tight around the rod’s circumference, they help keep out dust particles from the pipes during operation. They still maintain the constant pressure needed for critical jobs such as keeping fields irrigated. Ports create pathways through which liquids can travel, enabling smooth functioning and seamless performance over periods of long-term use.
Cylinder Barrel
The hydraulic cylinder’s major component is the seamless steel tube that contains the piston. The tube guarantees that the cylinder moves smoothly. It must be able to endure pressure and wear. It is strong enough for secure enclosing of the internal pressure zones. To guarantee its quality and durability in construction, honed tubes are used as part of high precision tolerance machining processes involving design, heat treatment, coating assembly, and testing stages before being implemented into use. In addition to providing strength against high pressures, fluid leakage is inhibited by primary seal placement inside the barrel. This indispensable element also provides the long lasting resilience necessary in any form of hydraulic system equipment application.
Piston
The crucial part of a hydraulic cylinder is the piston, which divides the pressure zones inside its cylindrical barrel to generate power and create linear movement. It attaches directly to the piston rod that carries this force onward to whatever load it needs to transfer to. The seal between itself and the walls must remain secure in order for optimal efficiency. O-rings, U-cups, or V-ring sealers guarantee such strength by attaching themselves tightly around threads on either end, connecting them both with bolts or nuts capable of enduring high stress levels.
Piston Rod
The cylinder rod, commonly referred to as the piston rod, is a significant element in the hydraulic cylinder assembly. This chrome-plated steel part links up the machine component to the cylinder so that work can be done through movement.
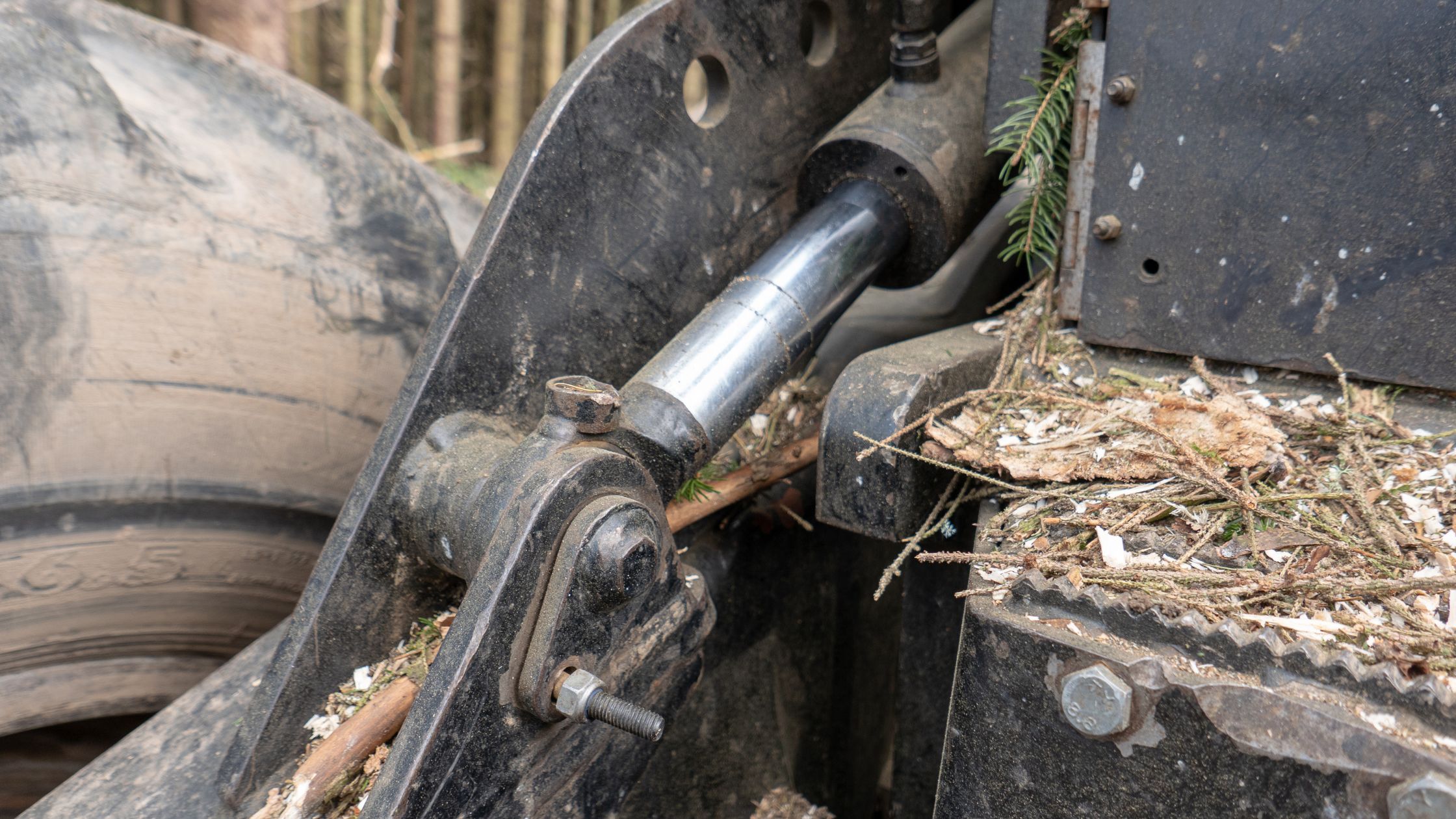
Polishing and finishing are necessary steps to ensure no fluid leaks occur, which might restrict the cylinder’s ability to operate. The piston rod also connects with a specific type of head, equipped with seals and bearings to help maintain pressure by preventing fluid leaks. These are all necessary elements when using precision machines or equipment to operate safely under extreme conditions.
Cylinder Head
The cylinder head is attached securely to the cylinder barrel with either an integrated rod sealing arrangement or a seal gland. It helps maintain the pressure inside by enclosing the pressure chamber at one end of the hydraulic cylinder and ensuring no fluid leakage. This yields optimum performance for that particular type of hydraulic system and prevents any potential damage due to lack of proper maintenance over time. These elements are necessary in maintaining reliability and efficiency.
Cylinder Base
The cylinder base connects to the barrel and secures it to mobile equipment, preventing any liquid from coming out of its sides. Common materials used when crafting this component are steel, cast iron, and aluminum. Rubber or plastic rings base create a secure seal between the piston rod, cylinder barrel, and end caps respectively. It is essential that these seals provide perfect fitting to prevent fluid leakage for optimal functioning of the hydraulic cylinders.
Seals and Glands
Seals and glands in hydraulic cylinders prevent fluid leaks and maintain pressure. It’s important to select the right material and design based on certain conditions, like cylinder working pressure, speed, operating temperature, etc. Elastomer nitrile rubber seals work best when it comes to lower temperatures. Fluorocarbon Viton seals are more suitable for higher temperatures. Knowing which seals best fit your needs helps ensure your cylinders will last long and provide optimal performance.
Ports
Hydraulic cylinders possess numerous ports that are engineered to ensure optimal performance and prevent hazardous leakage. These include NPT, SAE O-ring, pipe thread half coupling, and venting ports. The feature tapered seats and seals in order to secure fluid flow while reducing the risk of leaks. Consequently, proper port design is important for ensuring safe operation within a hydraulic system. Without it you may be at risk of potential leakages or inefficient performance.
Types of Hydraulic Cylinders
When it comes to selecting the correct hydraulic cylinder for an application, there are several types available. It is important to understand which type best fits a given project and its advantages over the others. Options include single-acting cylinders, double-acting cylinders, telescopic cylinders, and tandem cylinders. Let’s take a look at each one in detail so you can choose one that suits your needs effectively.
Single-Acting Cylinders
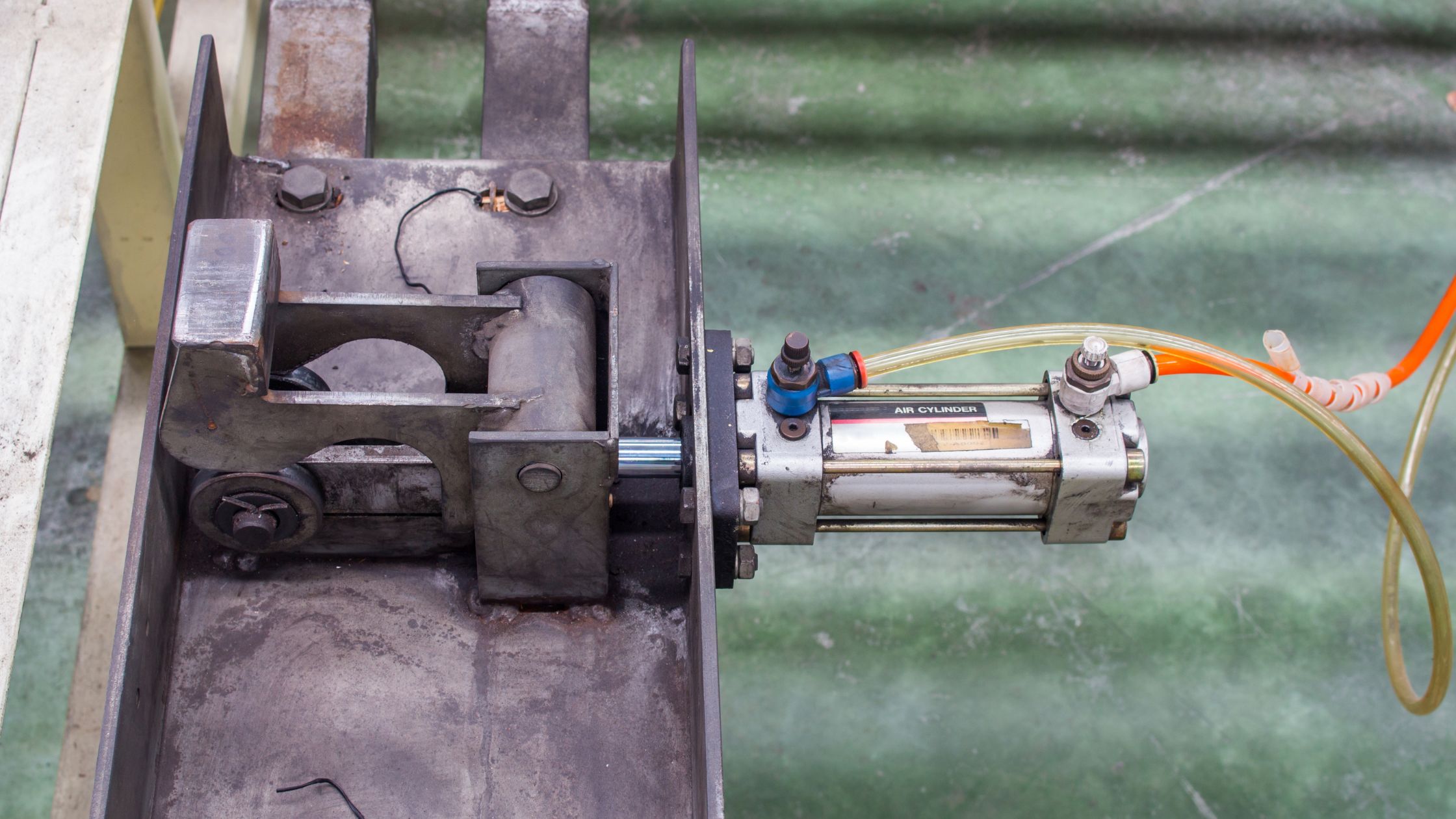
A single acting hydraulic cylinder uses pressure on only one side when operating. It utilizes energy from liquid or gas within the chamber. The force pushes against it until equilibrium is reached then locks into place afterwards. This is the ideal cylinder for linear motion operations such as elevator lifts, or presses like baling equipment found in recycling centers or paper plants.
Single-acting cylinders are a reliable solution for numerous practical applications due to their simple and cost-effective design. A pressurized fluid is passed through one port into the cylinder, causing the piston inside to extend.
When pressure is removed from this single acting system—through an external force like gravity or a spring—the piston retracts. These types of cylinders have been used successfully within industries such as food production, forestry work, motorway repairs, and wellhead control systems where precision engineering processes require simplicity and ease of operation.
Double-Acting Cylinders
A double-acting hydraulic cylinder works by using pressurized fluid in two separate chambers to drive the piston. The direction of movement is controlled via a valve system, allowing for precise and bi-directional control. These cylinders are ideal for many different applications in manufacturing, water control systems, and construction equipment.
When one port is activated with pressure, it pushes the piston, extending the cylinder. Activating another port does so in reverse, retracting that same part again, this time back into its original state. The process provides an incredibly versatile solution compared to single acting alternatives.
Telescopic Cylinders
Telescopic cylinders are an ideal choice when limited space is a factor, due to their single-acting nature and compact design. The stages of these cylinders can be extended sequentially by supplying hydraulic fluid. This grants them the ability to lift heavy loads with a long working stroke. Such models are popularly used in dump trucks, hauling equipment, and dump trailers.
Tandem Cylinders
Tandem cylinders are an ideal solution in certain situations where one hydraulic cylinder may not provide sufficient force or stroke length. These powerful systems consist of two barrels and piston rods, working together to generate a high amount of power within a limited area.
When combined with other types of cylinders, even more force can be produced with increased efficiency. Tandem cylinders have many practical applications in construction sites and production lines, as well as in machinery operations. They offer great versatility and deliver much stronger output than single-cylinder models could ever manage.
Summary
Understanding each cylinder’s qualities can help you pick the one that best fits your application. Regular upkeep, troubleshooting with industry experts, and talking to reputable vendors will lead to great performance from these cylinders. Knowing all there is about parts of a hydraulic cylinder guarantees that you maximize the potential of your equipment’s hydraulics!